Caratteristiche e applicazioni
Il mercurio, unico
metallo liquido a temperatura ambiente, sin dall'antichità più
lontana, ha suscitato curiosità e interesse. In particolare fu al
centro della curiosità e dell'interesse dell'alchimia, una
disciplina teorica e applicata, che aveva per fine precipuo la
trasformazione dei metalli vili in metalli preziosi. L'alchimia
conobbe la sua stagione più florida durante il medioevo e fino al
rinascimento, quando però dovette lasciare il posto alla chimica
che, pur raccogliendone l'eredità, seppe marcare delle profonde e
insanabili rotture. Infatti, mentre l'alchimia mirava ad una
conoscenza globale e intuitiva del mondo e subordinava i propri
risultati al consenso ed all'azione di potenze extra umane, la
chimica si appoggia esclusivamente su basi razionali e quantitative.
Le origini dell'alchimia
vengono fatte risalire a Ermete Trismegisto, un sapiente vissuto in
Egitto duemila anni prima di Gesù Cristo, ma molto probabilmente il
suo nome trova origine nella fusione dei nomi di due divinità, una
greca, Ermes (o Mercurio per i romani), ed una egiziana, Toth (Trismegisto,
infatti tris mega Toth = tre volte grande Toth). Il procedimento
metallurgico specifico dell'alchimia mirava alla trasmutazione di
metalli come il piombo, in argento con una operazione chiamata
piccolo magistero, o in oro, grande magistero. Per quel che riguarda
il mercurio ed il suo ruolo nell'universo alchemico, occorre
ricordare che esso fu considerato "anima" di tutti i metalli, e fu
al centro di tutti i tentativi alchimistici di ottenere l'oro, come
sostenne di essere riuscito a fare il francese Denis Zachaire, che
pagò con la vita il segreto del suo procedimento. Nomi utilizzati
anticamente per indicare il mercurio sono argentovivo e idrargirio o
hydrargyrum in latino, (Hydrargyrum è il nome da cui deriva il
simbolo Hg del Mercurio) che a sua volta deriva dal greco
hydrargyros, composto da ù5cop, "hùdor" (acqua) e apyupoc;, "àrgyros"
(argento).
Il mercurio trova
principale impiego nella preparazione di prodotti chimici
industriali e in campo elettrico ed elettronico. Viene usato nei
termometri, barometri, sfigmomanometri, coulombometri, pompe a
diffusione e molti altri strumenti da laboratorio, scelto perché
liquido, opaco e di alta densità. Tra i suoi impieghi in campo
elettrico ed elettronico rientrano la realizzazione di interruttori,
elettrodi, pile. In campo medico, l'amalgama di mercurio con altri
metalli è usato per realizzare le otturazioni dentali. Nelle "celle
a mercurio" viene utilizzato un elettrodo di mercurio liquido per
condurre l'elettrolisi del cloruro di sodio in acqua, per produrre
cloro gassoso e idrossido di sodio.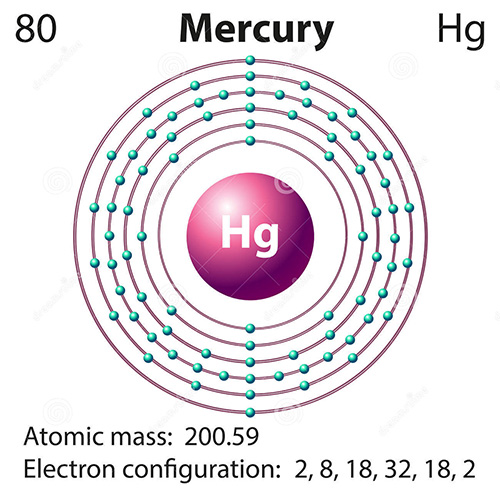
Il mercurio è stato usato anche come liquido di raffreddamento in
alcuni tipi di centrali elettronucleari e per realizzare telescopi a
specchio liquido. Il mercurio ha trovato impiego anche nella
purificazione dei minerali di oro e argento, attraverso la
formazione di amalgame.
Questo utilizzo, altamente inquinante e nocivo per l'ambiente e i
minatori, è ancora diffuso nelle miniere d'oro del bacino del Rio
delle Amazzoni, in Brasile.
I vapori di mercurio sono usati in alcuni tipi di lampade a
fluorescenza.
Grazie alla elevata tensione superficiale è un liquido che non
penetra nelle porosità aperte dei comuni materiali da costruzione.
Questo permette di misurare la distribuzione della porosità aperta
dei materiali mediante porosimetria ad intrusione di mercurio.
Ancora più vasti sono gli utilizzi dei composti chimici del mercurio
come catalizzatori, coloranti, insetticidi. Molti degli usi comuni
in passato, compresi erbicidi e farmaci, sono stati abbandonati per
la tossicità del mercurio.
Nel corso del XX secolo la produzione mondiale di mercurio ha subito
un aumento mai registrato nei secoli precedenti.
Le cause della sua
crescita sono da rintracciarsi soprattutto in un ampliamento delle
utilizzazioni di questo metallo, in una maggiore richiesta da parte
dei settori industriali che tradizionalmente lo usavano e nel
miglioramento delle tecnologie di estrazione.
Nel primo caso una elevata domanda di mercurio è giunta
dall'industria elettrica. Le caratteristiche fisiche del metallo,
elevato peso specifico ed alta conducibilità elettrica e termica, ne
hanno infatti consentito un vasto uso nella produzione di lampade a
vapori di mercurio, nonché interruttori, raddrizzatori, manometri e
contatori. Anche l'industria chimica nata come quella elettrica alla
fine del XIX secolo e diventata strategica negli anni tra le due
guerre mondiali, ha contribuito notevolmente ad aumentare la domanda
mondiale. Il mercurio è servito come base nella produzione di
numerose vernici, di vari insetticidi e soprattutto nella
preparazione di alcune tipologie di esplosivi. Non si deve infine
dimenticare l'estensione del suo utilizzo nei processi elettrolitici
di produzione del cloro e della soda caustica.
Tra le varie industrie chimiche, quella farmaceutica ne ha fatto un
abbondante uso nella preparazione di disinfettanti e, negli anni
trenta del ventesimo secolo lo ha usato massicciamente come base di
medicinali, soprattutto disinfettanti, destinati a combattere la
sifilide e varie patologie di natura parassitaria come la scabbia e
la tigna. I settori che tradizionalmente avevano fatto uso del
mercurio, come quello, metallurgico, hanno contribuito all'aumento
della domanda internazionale.
Poiché questo minerale ha la capacità di amalgamarsi con numerosi
altri è stato usato copiosamente nella preparazione dei metalli.
Tranne il ferro ed il nichel tutti i minerali sono attaccati dal
mercurio; la reazione chimica che si sviluppa dà luogo ad un
amalgama, dal quale si riesce più facilmente ad estrarre il metallo.
In particolare questo processo è stato usato massicciamente nel
processo con cui si ricava l'oro e l'argento. La risposta data a
questi incrementi di domanda ha portato nel corso del XX secolo ad
un aumento delle ricerche minerarie e all'attivazione di altri
giacimenti accanto a quelli tradizionali. Così, alle vecchie miniere
di Almadèn in Spagna, di Idria in Istria e di Abbadia San Salvatore
in Italia, si sono aggiunti progressivamente quelli di Nikitowka in
Russia e quelle nella Repubblica Popolare Cinese, nonché altri
giacimenti più piccoli in California, nel Messico e in Perù.
All'interno della
produzione mondiale le miniere di Abbadia hanno rappresentato,
almeno fino agli anni sessanta, una di quelle più importanti.
Tuttavia dopo una fase di ascesa della produzione che ha raggiunto
il suo apice massimo negli anni '50/ '60, altre realtà minerarie si
sono affacciate sul mercato internazionale, riducendo la quota
percentuale di produzione delle miniere toscane. Queste nuove
realtà, sorte in contesti meno tutelati dal punto di vista delle
condizioni di lavoro, hanno potuto contare su costi di produzione
inferiori, portando ad una progressiva dismissione delle miniere
toscane tra le quali quella di Abbadia San Salvatore.
Impianto
Metallurgico: i primi forni
Nel processo metallurgico
finalizzato ad ottenere il mercurio dal cinabro, sono stati
utilizzati nel tempo due soli metodi: I - distillazione
2-arrostimento.
Il processo di
distillazione era basato sulla riduzione del cinabro per mezzo della
calce viva o del ferro (in pezzi o limatura) entro recipienti
chiusi, riscaldati esternamente. Il mercurio, che si svolge in
vapore, esce sotto pressione, passa nei condensatori e si raccoglie
sotto l'acqua allo stato metallico.
Il processo di arrostimento, può applicarsi in mucchi, in forni a
tino (o a torre) e in forni a caduta. Il processo di ottenimento del
Mercurio dal Cinabro, unico solfuro semplice di mercurio da cui è
possibile estrarre in modo economico il metallo stesso, prevede
l'arrostimento del minerale all'interno di forni; a circa 500-600 °C
il mercurio sublima, passa cioè dallo stato solido a quello gassoso.
L'estrazione del mercurio dal suo solfuro (HgS), veniva compiuta
all'aria aperta.
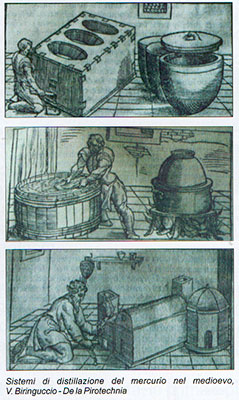
Il cinabro frammentato
era introdotto in vasi poi chiusi con muschio, capovolti, incastrati
su altri vasi e interrati in prossimità del fuoco. Il calore
provocava una reazione chimica che produceva mercurio puro allo
stato gassoso. Il raffreddamento successivo causava la caduta dal
vaso superiore a quello inferiore del mercurio che, filtrato dal
muschio, passava allo stato liquido. Già nel Medioevo, lo scienziato
senese Vannoccio Biringuccio, aveva dedicato per primo nel suo De la
Pirotechnia una forte attenzione agli effetti nocivi del mercurio:
"Ha proprietà di contrarre li nervi a quelli artefici che lo
estraeno de la miniera, se non son molto cauti, et a quelli che
longamente manegiando il pratticano, fa tutti li lor membri deboli e
paralitici".
Ad Almaden, dal '500 fino
ai primi decenni del XX secolo, è stato usato il forno Bustamante, a
sezione circolare, con il focolare nella parte inferiore e la camera
di distillazione nella parte superiore, dove si caricava il cinabro.
I condensatori erano costituiti da tubazioni in terracotta. Il
mercurio colava dalle tubazioni e, attraverso appositi fori, finiva
su un pavimento inclinato. Questo tipo di forni non poteva
funzionare in estate, a causa della elevata temperatura esterna che
danneggiava il processo.
Nel 1782 nella Miniera di
Idria si cominciarono a sperimentare le prime camere di
condensazione che, nonostante i perfezionamenti apportati nel 1842
da Glovacki, mantenevano un elevato rischio di intossicazione.
Restava ancora aperto, e difficile da risolvere, il problema della
cottura del cinabro. I forni erano ancora primitivi, fortemente
nocivi e inquinanti, e soprattutto incapaci di eliminare le elevate
perdite di mercurio metallico prodotto con una notevole scarsità di
raccolta.
Il primo forno istallato nell'area del Monte Amiata è stato
realizzato presso Selvena, nella contea di Santa Fiora nell'anno
1738 dal chimico e naturalista di Camerino Stefano Mattioli. Venne
poi descritto dal celebre naturalista Giorgio Santi che lo poté
osservare nel corso dei suoi viaggi per le terre di Toscana alla
fine del Settecento. Questo fornetto doveva produrre circa 3000
libbre di mercurio metallico all'anno e seguiva una procedura non
molto dissimile dal tradizionale metodo della distillazione
descritta a metà del '500 nella Pirotechnia di Vannoccio Biringuccio.
La tecnica impiegata si rifà, dunque, ad un ambito storico e
tecnologico ben più antico e lascia supporre l'esistenza di una
lunga tradizione nell'uso delle risorse cinabrifere di Selvena. Già
nel XIII secolo infatti, alcuni documenti parlano dell'esistenza di
una argenteria de Silvena, all'interno del grande patrimonio della
casata Aldobrandesca.
Il forno risultava costituito da due parti divise da una lastra in
peperino.
Nella porzione superiore del forno veniva disposto il minerale
ricco, precedentemente ridotto in pezzi di varia misura, attraverso
un'apertura della volta poi sigillata con un rivestimento di
argilla. Nella porzione inferiore veniva lasciato lo spazio per
accendere il fuoco, a
cui
era assicurato adeguato sfogo e ventilazione attraverso alcune
aperture laterali praticate nelle pareti del forno. La metà
superiore era chiusa da una volta ottenuta mediante l'incastro
perfetto di più pezzi, tutti sigillati per mezzo di argilla, o
lutati, e collegati, attraverso un'apertura circolare al sommo della
volta, ad una serie di manicotti in argilla di diametro decrescente,
anch'essi incastrati e lutati l'uno con l'altro, ed inclinati
opportunamente.
Questa piccola ciminiera terminava con due estremità, la prima e più
grande in asse con i pezzi precedenti, la seconda aperta ed
affacciata su un pentolo pieno d'acqua.
Una volta acceso il fuoco nella metà inferiore del forno, per
effetto del calore si otteneva l'evaporazione dello zolfo e la
formazione di vapori ricchi in mercurio.
Quest'ultimo, raffreddandosi nel percorso creato dai tubi in
terracotta, in parte si raccoglieva in forma liquida all'interno del
recipiente finale, ed in parte si fissava ai tubi stessi. Da qui
veniva asportato mediante l'introduzione di un apposito palo armato
di un cencio attraverso l'altra apertura alle estremità della
tubatura. Il processo di arrostimento delle glebe cinabrine durava
in media dodici ore.
Durante questo periodo si poteva procedere all'apertura laterale
della cupola per muovere i pezzi e favorirne l'arrostimento, ed
anche per inserire nuova materia prima.